According to the recently released Commercial Construction Index (CCI), an economic indicator that tracks trends in the commercial construction industry, demand for modular construction is on the rise, and general contractors expect the trend to continue.
Modular construction uses prefabricated and preassembled building components that are built in a factory and shipped to the job site for assembly. They meet the same standards and use the same materials as a traditional building but, advocates say, they offer a range of additional benefits.
As reported by The National Real Estate Investor, over the last five years, the modular construction business has doubled in size to become an $8 billion industry. What amounts for the new interest? Previous studies have shown that increased productivity and lower costs are driving contractors to embrace modular construction. Now, with materials costs continuing to rise around the world, these potential savings have become even more critical. But they’re not the only issue. The CCI study found that more than 70 percent of surveyed contractors reported eight clear benefits of modular construction: increases in efficiency, productivity, safety, and quality; reductions in risk, cost, material waste, and construction times—an particularly important benefit for revenue-earning buildings whose owners want to start collecting rent as soon as possible.
[interstitial]
A few of those benefits go hand-in-hand with one another, but the report is promising for the industry. The nonprofit Modular Building Institute also predicts an increase in modular construction over the next few years. However, in their view, it’s not just the above-mentioned benefits driving change, it’s also the accelerating loss of skilled labor that will push the industry further toward industrialization and automation.
The reports are a potential boon for the industry, which hit some bumps during what might be called its “start-up” phase a few years ago. Notably, 461 Dean Street in Brooklyn’s Pacific Park development hit setbacks that included manufacturing disruptions, disputes, and delays that ultimately lead to a four-year construction period and giving it, as AN wrote at the time, “the dubious honor of having one of the most languid construction timelines for a tower of its size in city history.” The plan for more modular buildings in Pacific Park was abandoned, but, after the project got back on track, the building now stands as a model of the potential and the pitfalls of modular construction.
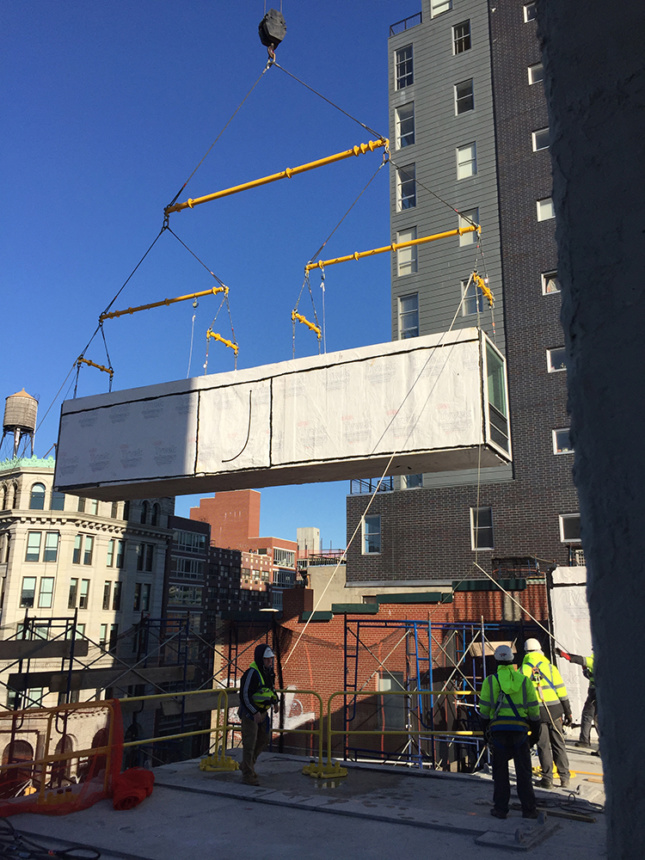
The stories that have since followed have suffered from fewer hiccups, like the 21-story CitizenM New York. The tallest modular hotel in the United States, the CitizenM is composed of 210 modular units, each housing two hotel rooms. Housing, hotels, and hospitals, which depend on the repetition of identical rooms and spaces, are the areas that stand to benefit the most and, in turn, drive the growth of modular construction.
What could stall the rise of modular construction? Upfront costs can be large and securing loans can be difficult. And although the manufacturing technology is becoming more sound, the much-touted savings aren’t as significant as predicted yet. That could change as demand rises, as more factories are built to produce modular components, and as other factors, like the use of autonomous vehicles to reduce shipping costs and advancements in BIM make it easier to build stronger partnerships between architect, fabricator, and contractor. The last hurdle? A lack of awareness. More than 70 percent of general contractors say their reason for not using modular construction is that clients aren’t asking for them and architects aren’t designing them.