There is a slide I like to show at the beginning of the architecture courses I teach that provides an overview of the last hundred years or so in design and technology. In the left column, a car from the beginning of the 20th Century (a Ford Model T) is poised over a contemporary car (a Tesla). The middle column contains a similar juxtaposition, showing a WWI-era biplane and a modern-day stealth fighter (an F-117A). In the right column, Walter Gropius’s 1926 Bauhaus Dessau building is seen next to an up-to-date urban mixed-use building. The punch line, of course, is that the two buildings—separated by roughly 100 years—look basically the same, whereas the cars and planes separated by the same timespan seem worlds apart. What is the reason for this?
Of course, a lot has changed in architecture in the last century, but many of those changes have happened at the material or technological level. In the close to two decades I’ve been practicing and studying architecture, I’ve had the fortune to work on many different types of buildings using many different types of material. I’ve worked with rammed earth at Rick Joy’s Tucson, Arizona, office, mass timber at LEVER Architecture in Portland, Oregon, and even built a museum in Los Angeles and a house in the Hamptons using FRP composites while at Diller Scofidio + Renfro. Each of these experiences—spanning different building typologies in different locations—has given me some perspective into the use of non-conventional materials in architecture, and about innovation in architecture in general. They have also shown that “material” and “technology” cannot be easily prised apart; even BIM is fundamentally a technology about managing materials and only secondarily about coordination and documentation. (In the following text, I will use them interchangeably.)
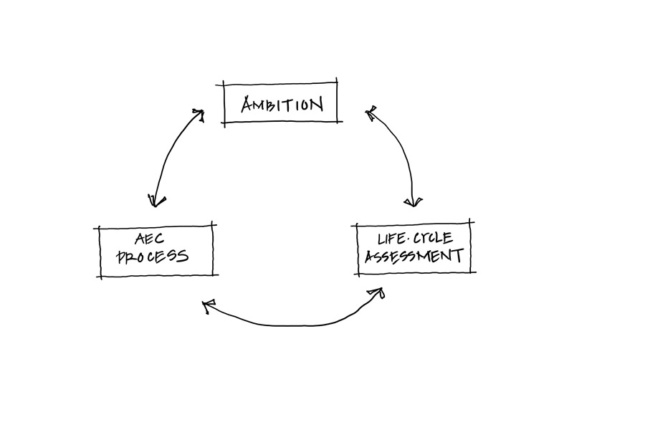
What’s Lacking and What’s Needed
What I’ve come to believe is that architecture lacks a rigorous framework for understanding, analyzing, and applying material innovation. While there is no shortage of sources for material inspiration in architecture—look no further than the cottage industry of coffee table books devoted to concrete, wood, and brick—a more complete discussion of material application is generally absent. Sources generally neglect one or more crucial considerations that directly correspond to viability in practical architectural usage.
By material innovation, I mean the development and application of materials and/or their technologies that lie outside conventional, codified construction techniques. Fantastic new technologies are being developed all over the world in various industries that may hold immense potential to improve our built environment. And yet, technology seems to come to architecture slowly. Notable exceptions include the mass timber being used throughout the Pacific Northwest or, to a lesser extent, carbon fiber, like that used at Apple’s Campus II and retail stores. These materials can seemingly offer striking new forms and architectural experiences, increase construction efficiency, and reduce environmental impact.
A more complete analytical framework for understanding architectural innovation could help assist those who currently work in the building professions as well as those currently outside it. In my experience, many promising technologies and/or materials are hampered by a lack of familiarity with the long and complicated building process; indeed, those wishing to enter into the relatively opaque nature of building and construction from the outside will face numerous obstacles—gaining an understanding of the building codes is just the first of many.

Applying an analytical lens
The framework I propose in my new book Composite Architecture (Birkhauser Architecture) is structured on three cornerstones of understanding: (1) architectural purpose or ambition, (2) AEC process, and (3) life-cycle perspective. The first, architectural ambition, follows from the premise that there is an incredible diversity of distinct and valid architectural ambitions that varies with uses, users, location, designers, and builders. This differentiates architecture from other products where the uses may be narrower and the goals more self-evident. The second cornerstone is a good grasp of the architecture, engineering, and construction (AEC) process, which, with its many different stakeholders, contributors, and constituents, can appear convoluted to outsiders; understanding where a material or technology fits into that collaborative process is crucial. The third cornerstone is an expanded life-cycle perspective that measures the impact of any material or technology from its genesis to its end-of-life (or, indeed, afterlife). Within such a view, any accounting of building materials or technology will have to factor in development, installment, use, and disassembly.
The three cornerstones presented here form a mutually reinforcing framework upon which architectural innovation can be studied, tested, and applied. A declaration of intent sets the cycle in motion, grounding all subsequent discussions about the suitability of any design, material, or technology. Furthermore, this context of ambition frames the communication for all the constituents and collaborators on a project.
Any prospective material or technology soon faces distinct challenges and opportunities as it runs up against considerations of (A) feasibility, (B) design and engineering, and (C) construction. In the feasibility phase, it is subjected to cost analysis and building codes, while efficient means of coordinating design, engineering, and fabrication parameters play a part in determining its viability. Even if viability is established, it can still be overturned by contractors for reasons of experience or logistics.
Assuming our material or technology has provided enough value up until this point, it must still be scrutinized according to its process of composition and development, regimes of operation and maintenance, and, finally, the potential for disassembly and reuse (its life-cycle).
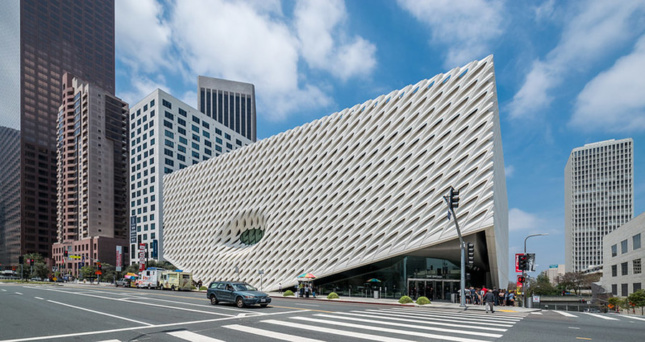
Making a Case
Let’s now apply the framework to a case study material—mass timber. As an alternative to structural concrete or steel, mass timber structures present many potential benefits. The most oft-cited benefit is ecological or environmental: Mass timber—an umbrella term for standardized wood-based building products including CLT, DLT, NLT, glu-lam, and mass plywood among others—is a renewable resource that represents a potential reduction in embodied energy or carbon footprint. This may be particularly true when compared to alternative constructions using steel or concrete, but these benefits are diminished or non-existent when measured up against those using light wood (stick) framing. The onerous structural demands of mass timber present another problem, and it has diminishing benefits in geographic regions distant from sustainably managed forests (where transporting the material and/or unsustainable resource management would negate some of the initial/embodied benefits).
Moving onto the feasibility phase, mass timber faces challenges from existing building regulations. The majority of current building codes in most U.S. jurisdictions allow for mass timber construction in only a limited number of cases. While this is changing quickly, due in part to concerted lobbying efforts by those in the timber and wood industry, it remains a significant hurdle to obtain a building permit for mass-timber constructions outside of limited building typologies in those jurisdictions.
But additional benefits to mass timber use can be found in the construction phase, due to its ability to be partially prefabricated off-site. Again, this compares favorably with certain building types in certain situations, and less favorably in others.
The visual and aesthetic benefits of exposed wood accrue in the design and operational phases, provided that regulatory codes for the building typology proposed do not mandate the fire protection of exposed wood surfaces. This is the case in certain building types and sizes, negating any aesthetic benefit to mass timber in those scenarios.
This brief and concise application of the framework to the case of mass timber immediately yields several salient conclusions: In projects where certain ecologic ambitions are present; local material stocks are well-managed; jurisdictional building regulations are permissive; the alternative structural materials would be concrete or steel but not light-frame wood; there are available suppliers and installers, and a certain aesthetic is desired, mass timber may be appropriate.
So we can immediately ascertain the situations in which mass timber would be a meaningful, feasible, and effective vehicle to advance a certain ambition. But we can also quickly understand where the obstacles lie that would prevent wider-scale adoption of this technology and how to address them. For instance, advocates of mass timber need to address regulatory constraints, develop resources among suppliers and contractors in suitable locations, and argue for a prioritization of the specific ecological benefits it contributes.
Facilitating Innovation
This analytical framework can be applied to any material or technology—as indicated above, the two are often joined at the hip—to gain insights into its applicability, potential, and specific points of challenge within architecture and construction. Hopefully, it will help engender a more complete and sophisticated discussion of architectural materials and technology, both new and existing.
For instance, while mass timber is currently enjoying its moment in the sun, other materials like plastic find themselves on the opposite, downward end of the fashion cycle. The issue may be a misapplication of properties to appropriate uses. Durability and resistance to environmental degradation, which is a property of many types of plastic, is perhaps grossly inappropriate in single-use applications such as packaging or grocery bags. But that same property of extreme durability can be game-changing in the right applications. For instance, in civil infrastructural applications such as bridges and tunnels, the expanded durability and higher strength of advanced polymer composite materials should bear consideration—especially in comparison to materials with shorter lifespans and/or greater maintenance costs. The expanded perspective of a life-cycle assessment may illuminate benefits for certain non-conventional materials. For example, the extreme strength-to-weight properties of composite materials can provide novel architectural experiences, such as those achieved in the Apple buildings, and can benefit the projects where those ambitions are present.
In any case, the goal of the analytical framework proposed here is to help facilitate the development of material innovation in architecture. With a more complete and comprehensive analysis, we can begin to contribute to a more meaningful assessment of the suitability of new materials and technologies in our diverse building culture.
No analytic framework is ever complete, and the one that I am proposing is no exception. Each building and project team will have ambitions or considerations that are outside of those outlined here. However, the three-cornerstone method described above should provide a rough schema for coordinating development among those who do, and hope to, contribute to a more innovative future of building. This is relevant now, as much as it ever has been, given the changing nature of what, how, and why we will build in the future.
Quang Truong is principal and cofounder of Polytechnica and the author of Composite Architecture: Building and Design with Carbon Fiber and FRPs (Birkhauser Architecture, 2020). Prior to founding his own practice, he worked at LEVER Architecture and Diller Scofidio + Renfro, among other firms.