Just weeks after it announced a partnership with the Virginia Center for Housing Research at Virginia Tech to design, build, and study America’s first 3D-printed, private-public partnership grant-funded single-family home in Richmond, Alquist has revealed another unprecedented project underway in Williamsburg, Virginia. This time, it’s the East Coast’s first 3D-printed Habitat for Humanity dwelling.
The project, spearheaded by additive construction company Alquist with Habitat for Humanity Peninsula and Greater Williamsburg, will mark the second 3D-printed home in the United States for the Georgia-headquartered international nonprofit organization. The first was a 1,738-square-foot dwelling currently being constructed with a gantry-style Build on Demand Printer (BOD 2) in Tempe, Arizona. (Alquist is not involved with that Habitat Central Arizona-led undertaking.)
The timing for these two geographically disparate Habitat projects (and there are likely more to come) that rely on concrete as a primary building material is consequential as Habitat for Humanity, which is the largest not-for-profit homebuilder in the world, faces nationwide project slowdowns due to the astronomical price of lumber.
“As we continue our mission to build more affordable homes for the communities that need them most, Habitat for Humanity Peninsula and Greater Williamsburg is the perfect partner bringing our shared vision to life,” said Zachary Mannheimer, founder and CEO of Alquist, in a statement. “Using 3D printing allows us to speed up the construction of a home while also lowering building costs, solving two housing challenges at once: the rising price of new homes and the speed at which they’re built.”
Per Alquist, its sustainable, storm-resistant concrete homes cost roughly 15 percent less per square foot to build than conventional, stick-built dwellings.
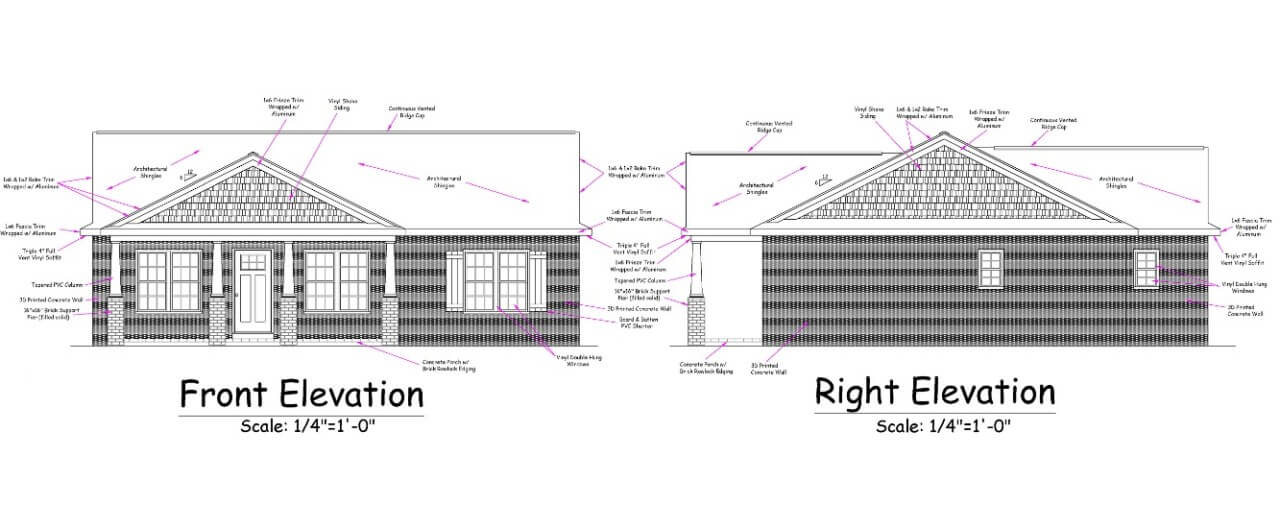
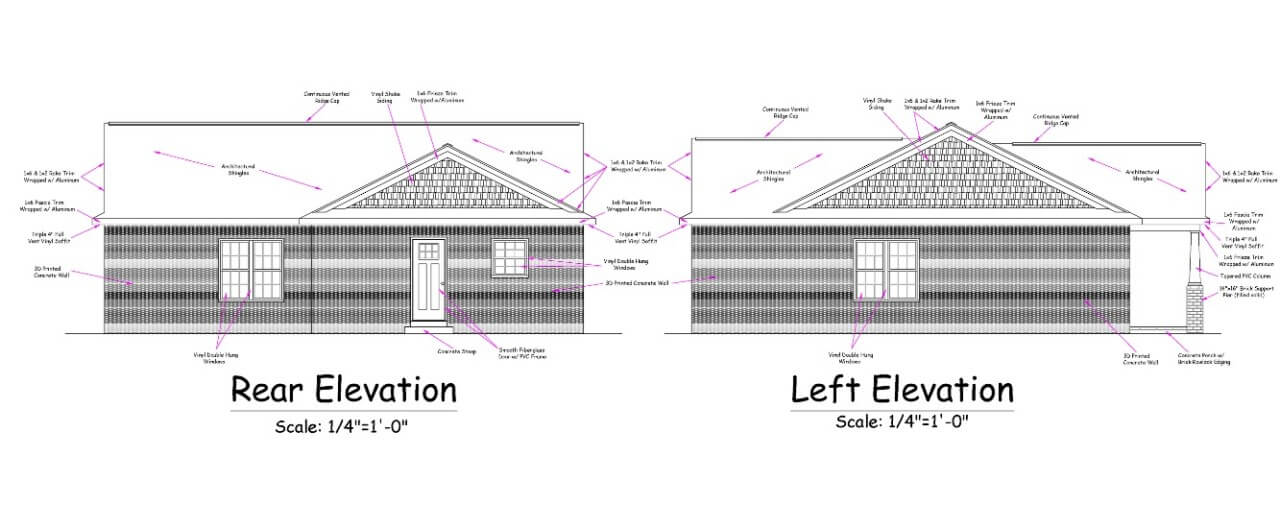
Alquist’s 3D-printed Habitat home in Williamsburg will be a 1,200-square-foot structure featuring three bedrooms, two full bathrooms, and a proprietary Raspberry Pi-based monitoring system developed by Virginia Tech. Like with all new homes built by Habitat for Humanity Peninsula and Greater Williamsburg, it will also be EarthCraft certified.
Ahead of the home’s construction, the Newport News-based Habitat for Humanity Peninsula and Greater Williamsburg selected a first-time homeowner named April who, as detailed in a press release, has worked in a local hotel for several years supervising its laundry facilities. Despite her steady employment, her income is less than 80 percent of the area median income, putting homeownership out of reach.
“Going forward, her monthly mortgage payments will be no more than 30 percent of her income, including her real estate taxes and homeowner’s insurance,” said Janet V. Green, CEO for Habitat for Humanity Peninsula and Greater Williamsburg. “Once the house construction is complete, she will close on her new home with a local attorney and repay her no-interest mortgage to us here at the local Habitat, illustrating Habitat for Humanity’s objective to give families a hand up rather than a handout.”
Once April and her family settle into their new 3D-printed abode at 123 Forest Heights Road in Williamsburg’s Ewell neighborhood, they’ll enjoy additional savings thanks to the state-of-the-art home monitoring system, which, among other things, help to optimize energy consumption, as well as from the thermal properties of the concrete structure itself.
Construction of the 3D-printed home’s interior and exterior walls is slated to kick off later this month and will be viewable via Habitat for Humanity Peninsula and Greater Williamsburg’s live construction cam.