Just a year after Austin, Texas–based construction technology startup ICON first unveiled a half-dozen 3D-printed homes at a 51-acre community established to provide affordable, permanent housing for formerly homeless residents of the city, the fast-growing (and Bjarke Ingels Group–backed) company has announced, in partnership with Kansas City, Missouri–based real estate developer 3Strands, the arrival of a new development in East Austin populated by two-to-four-bedroom homes that harness the same 3D printing construction technology as previous ICON structures. The key difference here is that ICON’s latest habitable 3D-printed creations, designed by Austin-based Logan Architecture, are the first to hit the “mainstream” real estate market with prices starting at $450,000.
This is a departure for ICON given that its earlier projects, including Austin’s aforementioned Community First Village and a low-cost housing scheme in Mexico, were affordable in nature. A press release refers to the single-family homes that compose 3Strands’ East 17th Street Residences in Austin as “America’s first 3D-printed homes for sale.” This claim, while impressive, should be taken with a grain of salt considering that in February, Long Island, New York–based SQ4D similarly boasted that its 3D-printed, single-family residence (asking price: $300,000) in Riverhead, New York, was the first “permitted” home of its kind in the U.S. to receive a certificate of occupancy and hit the open market via a multiple listing service. And before that, other developers and construction technology companies have made similar remarks in regard to their 3D-printed abodes.
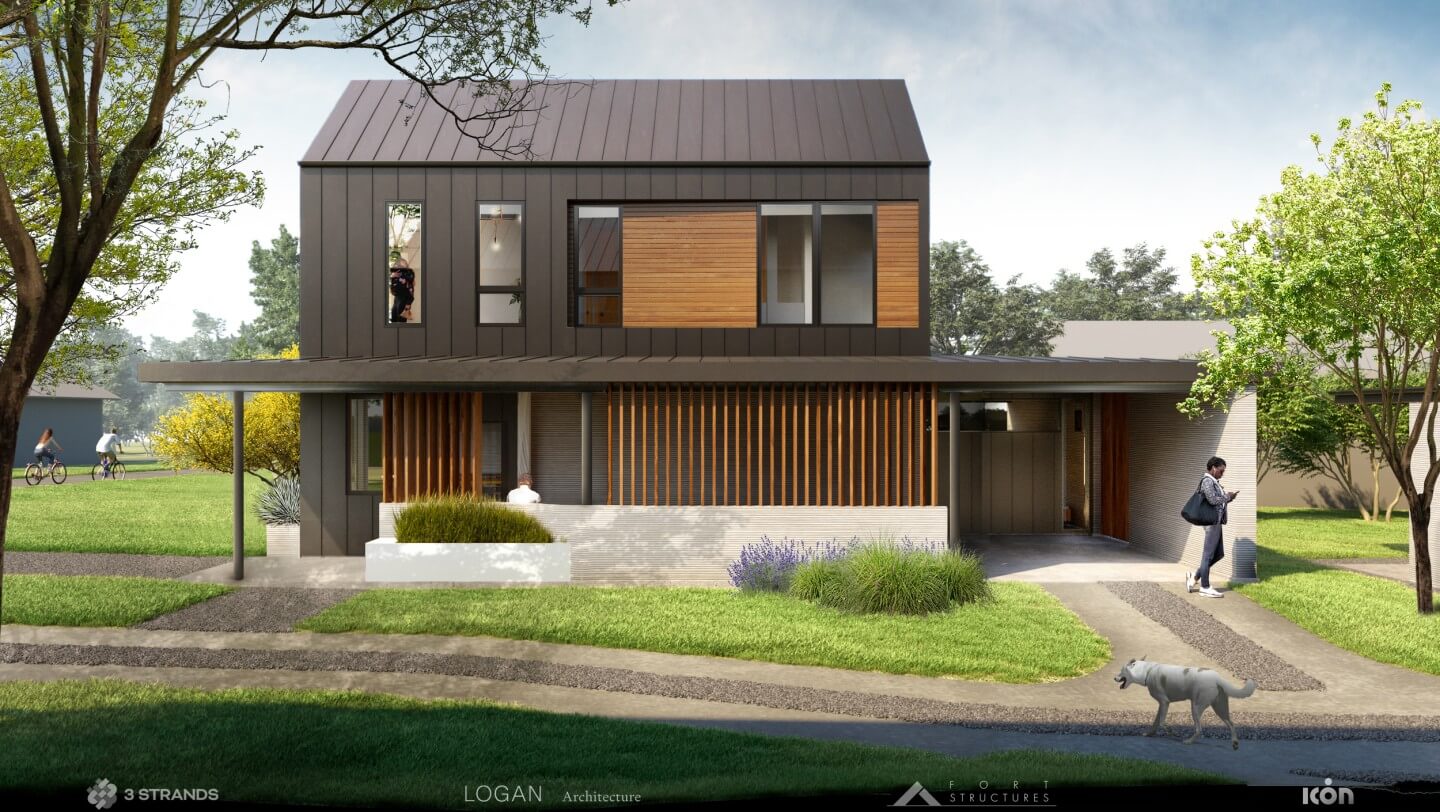
Matters of who was “first” aside, the near-completion of the East 17th Street Residences marks a major development for much buzzed-about ICON as it shifts from smaller and more experimental projects like the aforementioned Community First Village, a low-cost housing scheme in Mexico, and lunar accommodations into the mass market with bigger homes sporting bigger price tags.
“We want to change the way we build, own, and…live in community together,” said 3Strands cofounder and CEO Gary O’Dell in a statement. “This project represents a big step forward, pushing the boundaries of new technologies, such as 3D-printed homes.”
“ICON has delivered better homes at a better value across a variety of cost-centers than conventional construction, including materials, time to market, and labor,” O’Dell added. “The East 17th Street Residences represent the future of homebuilding for the mass market and illustrate what is possible with this technology.”
It’s worth pointing out that, in this instance, ICON’s proprietary Vulcan construction system didn’t produce structures that are entirely 3D-printed. Rather, these dwellings could be classified as hybrid structures: their first floors are indeed “printed” using a massive machine developed by ICON that extrudes a cement-like compound described as an “advanced material that is stronger and longer-lasting than traditional building materials.” Everything above, however, is constructed using conventional, stick-built methods. Still, the homes enjoy the same super-resilient perks—the 3D-printing technology enables the homes to better withstand “fire, flood, wind, and other natural disasters”—as their fully printed siblings.
With interiors ranging from 1,000 to 2,000 square feet, the energy-efficient East 17th Street Residences feature spacious open-concept floor plans, high-performance HVAC systems, attached carports, and large front porches that allow the homes’ residents to enjoy the outdoors while shielded from the sweltering Texan sun. The homes’ “bespoke interior design” comes courtesy Austin-based designer Claire Zinnecker who, according to a press release, employs a “modernized West Texas design with a simplified palette featuring natural woods, similar metal finishes, and earthy tile colors.”
“There is an extreme lack of housing that has left us with problems around supply, sustainability, resiliency, affordability, and design options,” said Jason Ballard, cofounder and CEO of ICON. “With ICON’s 3D printing technology, we anticipate more high-velocity progress in the years ahead to help bring housing and construction into the modern world and in-line with humanity’s highest hopes.”