Deep in the forests of Ithaca, New York, a short drive from the Cornell University campus, lies the newly completed Ashen Cabin, a practical example of how new manufacturing methods can turn what used to be waste into useful materials. The small cabin was built by HANNAH, the small practice headed by Leslie Lok and Sasa Zivkovic, assistant professors of architecture at Cornell (Zivkovic also heads the school’s Robotic Construction Laboratory, or RCL). When AN last visited in 2018, the cabin was still unenclosed; the project was assembled in two parts, with the first phase consisting of nine interlocking, 3D-printed concrete segments forming the footing, cabin floor, chimney, and interior fixtures. Each concrete component was printed without formwork by filling the pieces with aggregate while printing to ensure the wet concrete didn’t slide inward. It’s a method HANNAH has employed once before, in their 2018 RRRolling Stones seats at Socrates Sculpture Park.
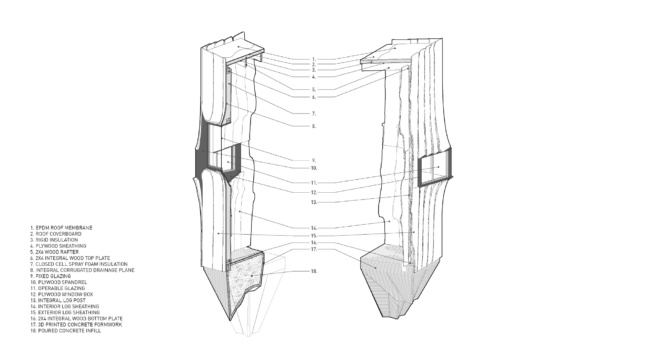
“We know that concrete is responsible for 8 [percent] of total CO2 emissions,” said Lok in a statement. “By using 3D printing, we eliminate the use of wasteful formwork and can deposit concrete smartly and only where structurally necessary, reducing its use considerably while also maintaining a building’s integrity.” For the second phase, the team repurposed a six-axis robot arm found on eBay to saw wood for the facade. The RCL team took 3D scans of irregularly-shaped Ash trees that had been killed by invasive Emerald Ash Borer beetles, and used the arm to slice their logs into pre-shaped planks that fit together and enclose the cabin like puzzle pieces. Typically, this type of wood would be wasted, as the non-standardized shapes render them useless for other construction purposes. The facade was then supplemented with more traditional window boxes, and the Ash facade backed by foam insulation.
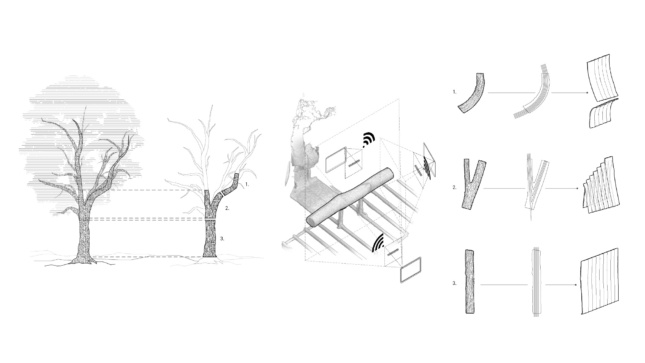
“Infested ash trees often either decompose or are burned for energy,” said Zivkovic in a press release. “Unfortunately, both scenarios release CO2 into the atmosphere, and so the advantage to using compromised ash for construction is that is that it both binds the carbon to the earth and offsets the harvesting of more commonly used wood species.” The team hopes that their approach can ultimately be scaled up to bring what would typically be thought of as “waste wood” into construction. While robotic fabrication is still a boutique manufacturing method, the repurposing of a robot arm already commonly used for assembling cars means that the potential to scale up is there. “Infested ash trees are a very specific form of ‘waste material’ and our inability to contain the blight has made them so abundant that we can — and should, develop strategies to use them as a material resource,” said Zivkovic.
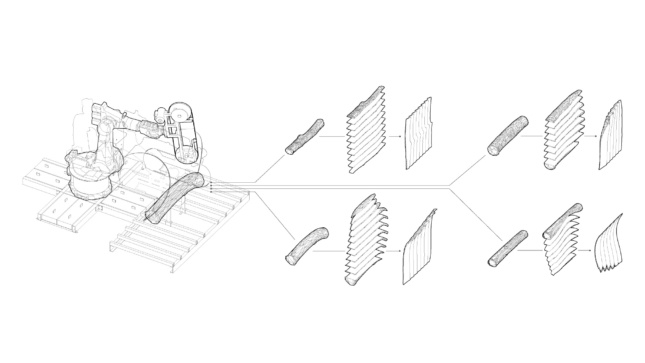
The RCL took a similar approach with LOG KNOT, a freestanding timber installation on Cornell’s campus that used a CNC mill to turn waste logs into a self-tensioning structure. The logs were 3D-scanned and cut into segments that were later lifted into place and bolted by hand, demonstrating the technique’s applicability for creating structural timber components.