Syracuse-based APTUM Architecture has designed and fabricated Thinness, an ultra-light concrete pavilion in collaboration with international concretemanufacturer Cemex Global R&D.
Concrete is one of the most ubiquitous construction materials in the world. Its advantages are many: it’s easy to produce, is remarkably strong, and can take on a variety of forms. It does, however, have one rather weighty constraint: it’s heavy. Thinness is an experiment in using contemporary and historical casting methods to create novel forms that stretch concrete to its thinnest and lightest proportions while maintaining structural integrity. The installation uses its shape and a proprietary concrete mix that includes glass beads for aggregate and steel fibers to create a freestanding structure with walls that are only three-quarters-of-an-inch thick.
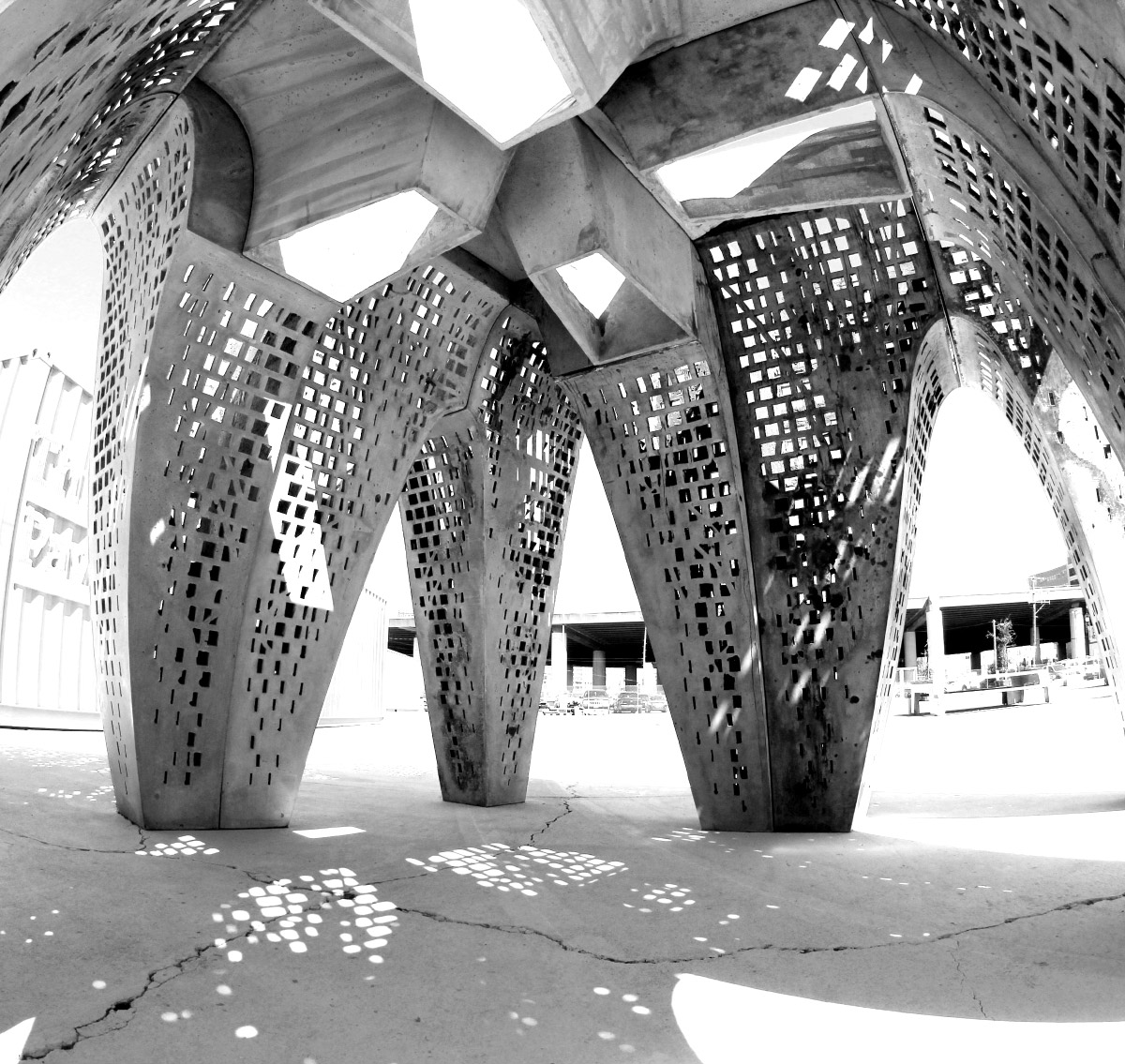
The perforated pavilion, a collection of 12 exterior columns arranged around four central light wells, was designed to be modular and scalable. The columns taper at the base and expand as they rise, vaulting to form a ring of arches. Although the installation is ten feet tall and ten feet long on each side, each column weighs only 200 pounds.
Architects Julie Larsen, Assoc. AIA, and Roger Hubeli, founding partners of APTUM and professors at Syracuse University, sought to explore “thinness” and the role of volume in architecture. In collaboration with the research and development department at Cemex, based near Monterrey, Mexico, the team was able to develop a fiber-reinforced concrete mixture that would evenly distribute around the form’s sharp corners without clumping and weakening the structure.
Grasshopper was used to map the stress across each column, and the perforations were made smaller or eliminated in the most heavily stressed areas to help distribute the load more evenly. The team ran through different pattern iterations looking for the correct balance between load-bearing ability, aesthetics, and amount of void before settling on the final grid.
The columns were cast using the lost-wax technique. First, a silicon mold was cut using a water jet, and then braced in a steel enclosure to protect against bowing as the concrete cured. Wax was then poured into the mold to form a freestanding column; the silicon formwork was then removed, and concrete was poured over the wax. Once the concrete was fully cured, the wax was melted and the process was repeated for the remaining components.
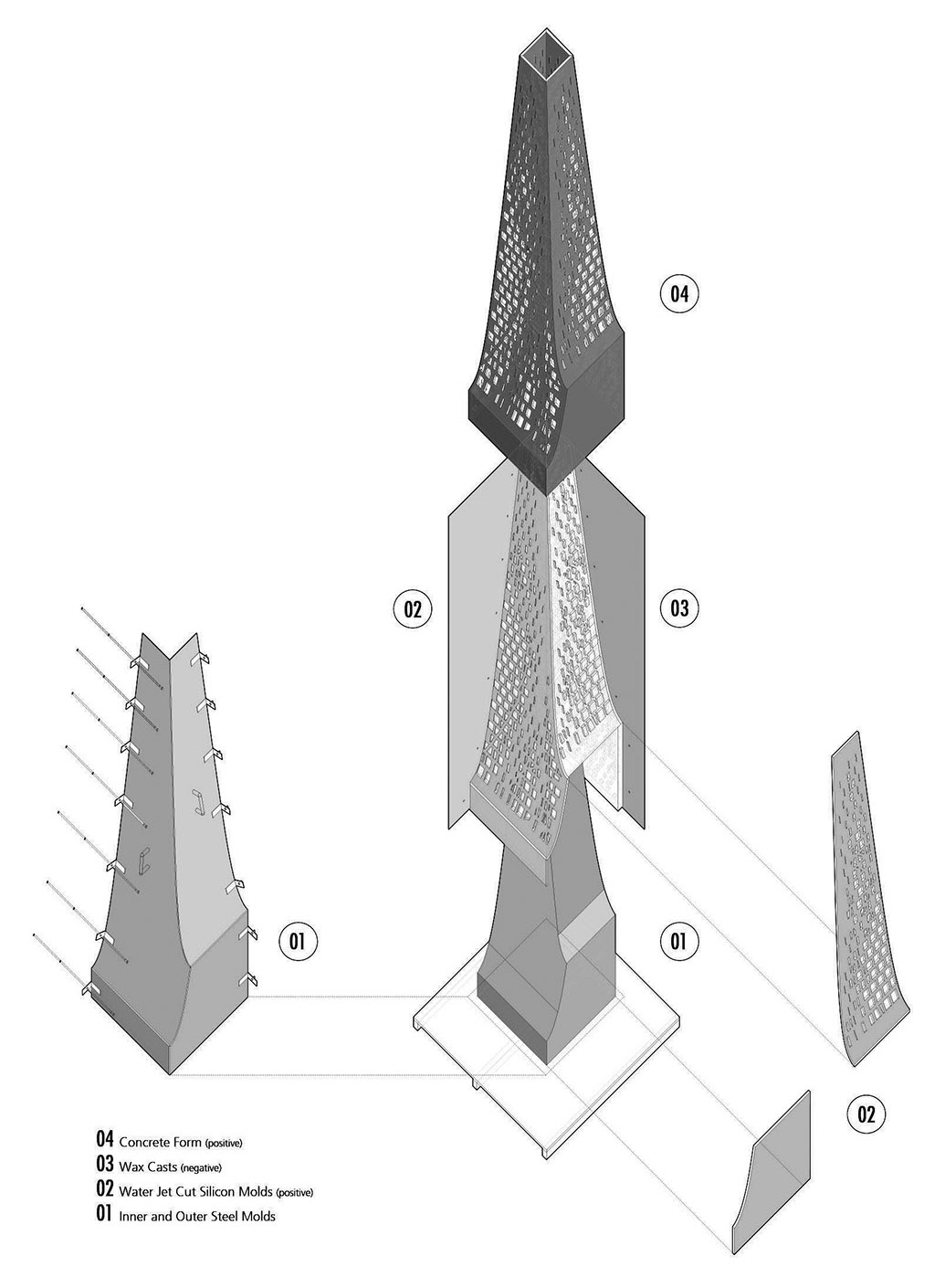
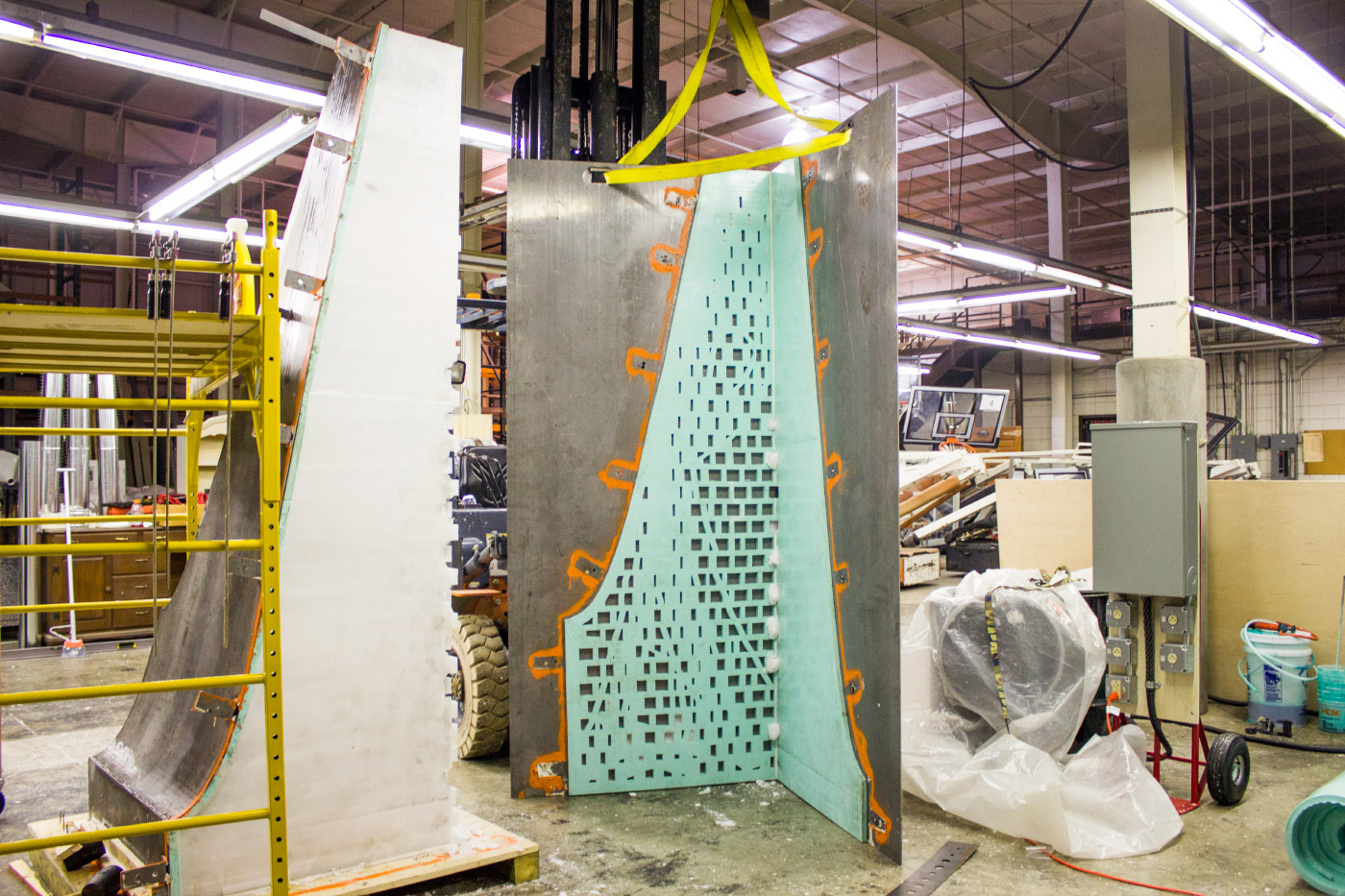
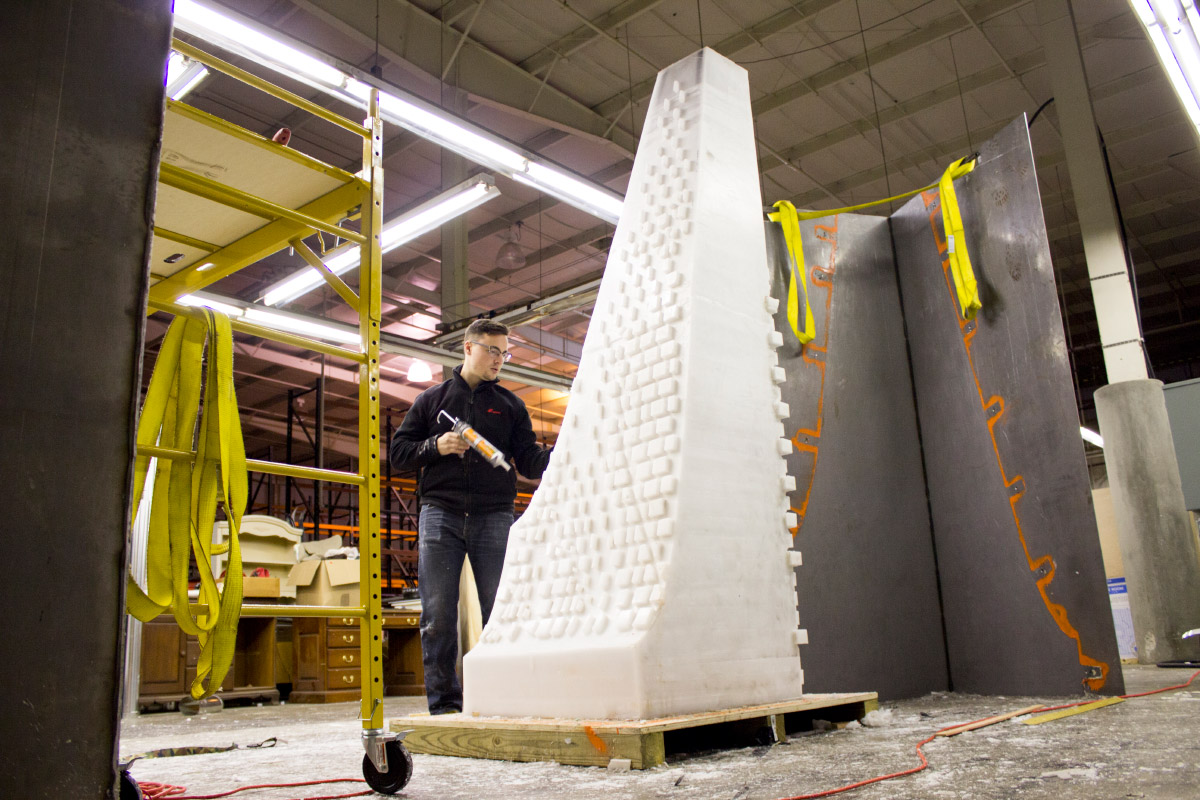
Thinness is just the first step in what Aptum sees as a collaborative, interdisciplinary future between academia and concrete manufacturers. In the future, APTUM wants to scale up the technology behind Thinness to encompass structural elements and has released a rendering of a speculative skyscraper made from the same components. Thinness was recognized with a citation in the AIA’s 12th Annual R+D Awards this year. The project was also on display at the Designing Material Innovation exhibition presented by the California College of the Arts earlier this year.
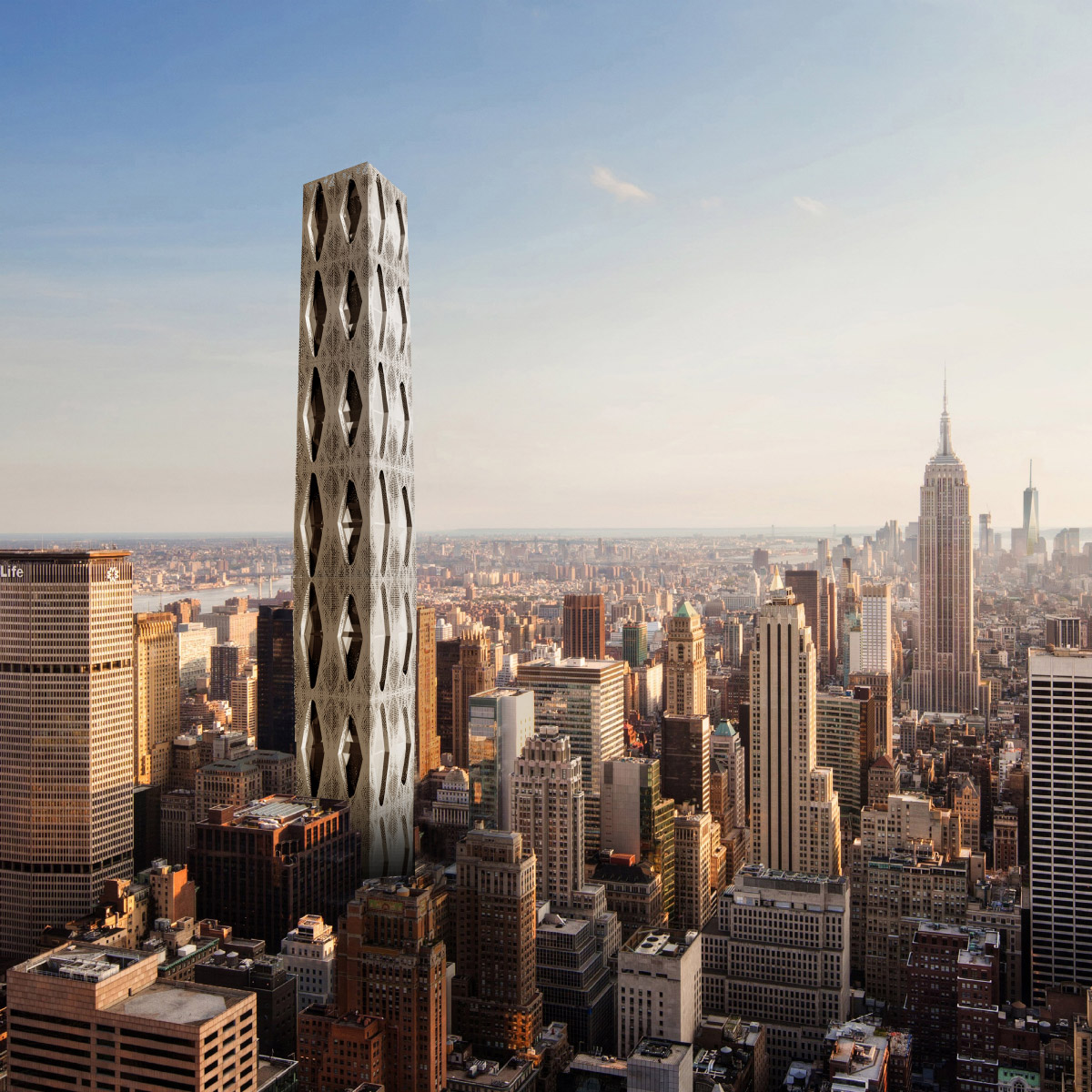
Design Firm: Aptum Architecture, Syracuse, N.Y., Roger Hubeli, Julie Larsen, Assoc. AIA (project team)
Industry Partner: Cemex Global R&D, Davide Zampini, Alexandre Guerini, Jeremy Esser, Matthew Meyers (project team)
Fabricator: Cemex Global R&D
Structural Engineer: Sinéad Mac Namar
Research Assistants: Sean Morgan, Ethan Schafer